MBI Eagle 3 Rotating Scrap Shear
The MBI Scrap Shear 3 is a cut above the rest. Also known as metal cutting shears, scrap metal processing shear, hydraulic shears or metal recycling shears, this powerful and durable demolition tool is engineered for optimal performance.
With a compact frame and an oversized, inverted cylinder, the MBI Scrap Shear 3 provides up to 30% more cutting force. With the innovative jaw design it also allows for 9% wider jaw opening, allowing for even the most complex task to be tackled.
Both fixed and rotating versions are available.The shear comes with a replaceable HARDOX 500 front shield, as well as HARDOX 500 armoured plates on areas that are prone to wear and tear, improving the durability and longevity of the attachment.
The jaws are also constructed with HARDOX 450 steel so you can be sure it can handle even the most demanding project.
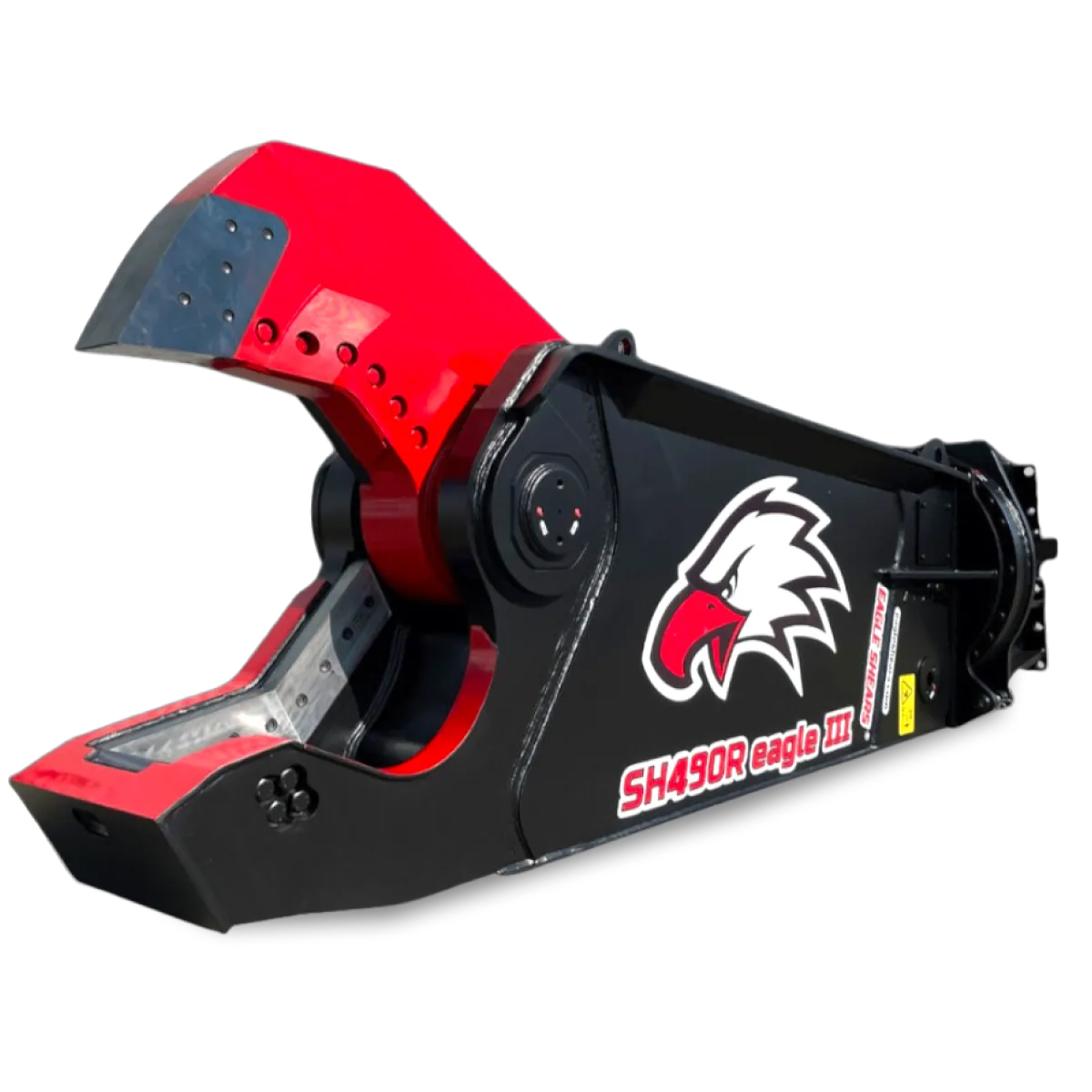
Product Features
The MBI Scrap Shear 3 features up to 30% more cutting force due to the new jaw design. It also allows for a 9% larger opening. This enhances cutting capabilities and allows operators to work more effectively, tackling more complex tasks with ease.
The oversized cylinder features an innovative inverted design that protects the rod inside, while the enlarged bore generates more power by accelerating the opening and closing of the jaws. This provides superior reliability and reduces maintenance with quality seals lasting up to 3,000 hours.
This technology significantly reduces opening and closing times of the shear. It does this by optimising the hydraulic flow to allow for efficient and smooth operation. Along with faster cycle times, the speed-valve also reduces wear and tear on the attachment, leading to lower maintenance costs.
This innovative design offers a smaller design and contains a unique weight-performance ratio but moving the centre of gravity of the shear to the rear. This improves the stability of the excavator, making it more balanced and improving ease of operation.
The most heavily used areas of the shear are reinforced with interchangeable HARDOX 500 steel armour plates to have added protection, increasing the shear’s lifespan. This ensures high wear resistance, while maintaining consistent performance during even the most demanding tasks.
The double cutting guide is essential in maintaining jaw alignment, thus increasing the potential cutting power of the shears. Operators can easily check and fine-tune the alignment over time.
How to Install
See It in Action

Smart Connect
Built For a Wide Variety of Applications
Learn More
Rock Breaker Reviews
Google with a rating of 4.7/5!
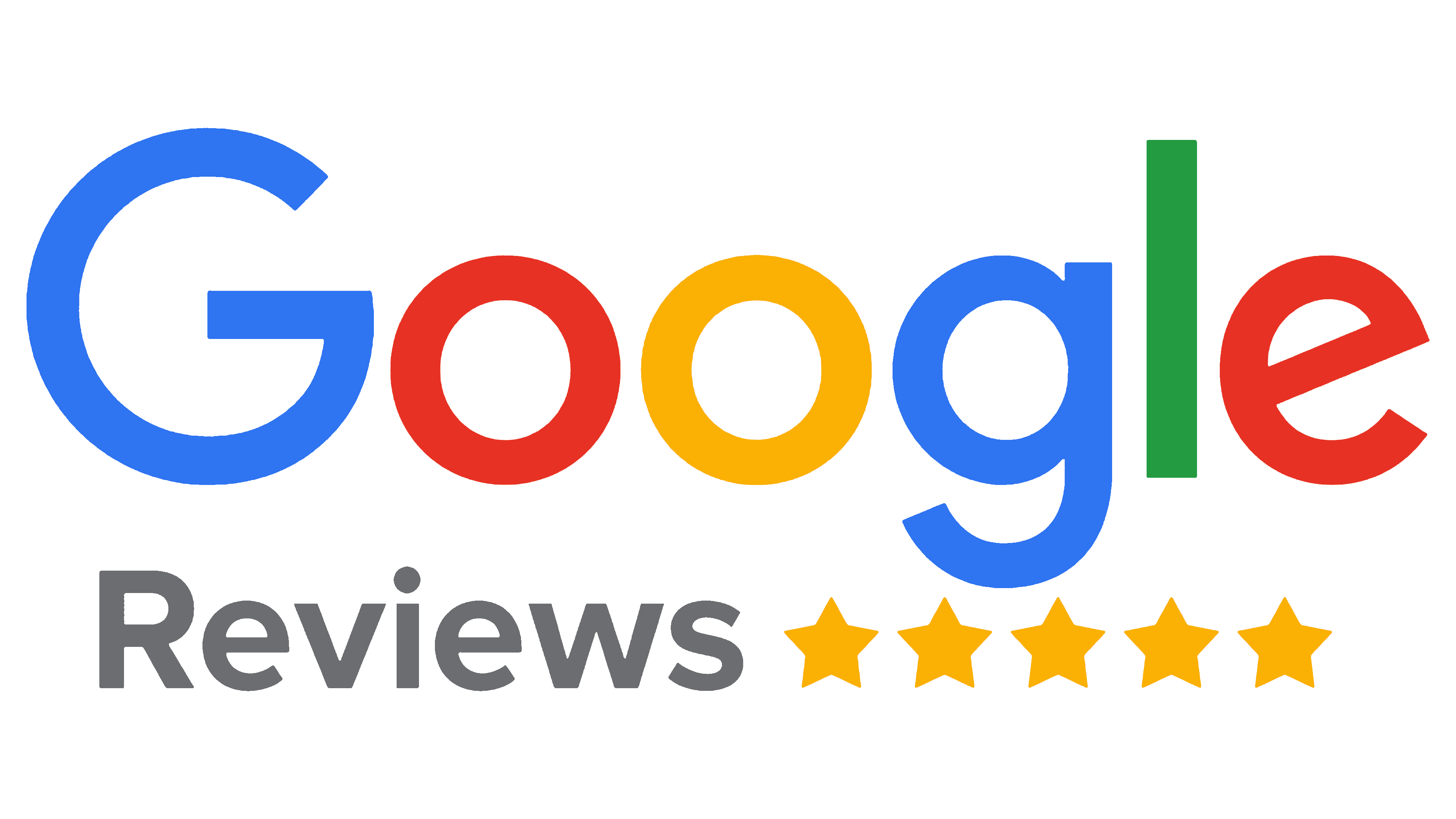
Rock Breaker FAQs
Designed in
Australia, for
Australia
Meet the Aussie Buckets Tilt Rotator. It’s the first on the market to use a standard Australian hitch, so you can keep your existing attachments while enjoying unlimited 360° rotation, 45° tilt each side, and integrated grabbing, all in one.
MBI Eagle 3 Rotating Scrap Shear
Enhance your excavator’s capabilities with our cutting-edge Tilt Rotator, also known as a Rotating Tilting Hitch. The Aussie Buckets Tilt Rotator offers unlimited 360-degree rotation with a 45-degree tilt on each side and an in-built optional pincer grab, giving operators maximum flexibility to tackle complex angles, precise positioning, and added versatility.
Designed with compatibility and cost-effectiveness in mind, this is the first Tilt Rotator on the market that uses the standard Australian hitch. This allows existing attachments to integrate seamlessly, reducing unnecessary costs and simplifying the setup process. Ask ChatGPT Featuring our innovative locking system with three mechanical safety locking points, it provides exceptional safety and peace of mind while meeting all Australian quality and compliance standards.
*Pictured model: 10-17 T Tilt Rotator
Smart Features for Smarter Operations.
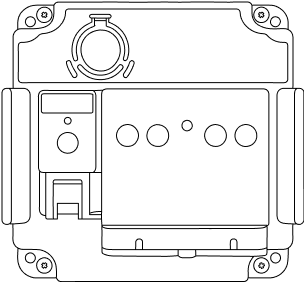
Smart Control Unit
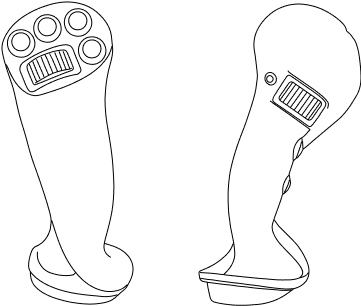
Configurable Joysticks
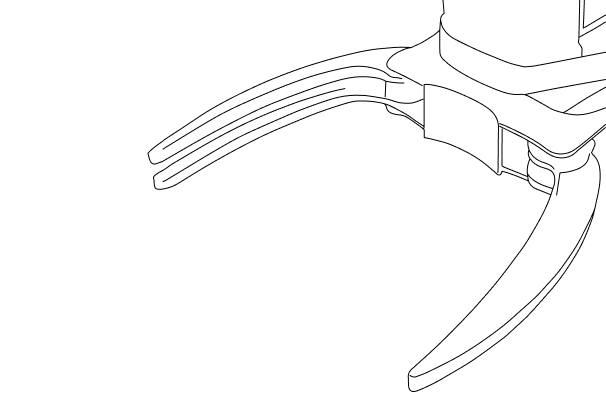
Pincer Grabs
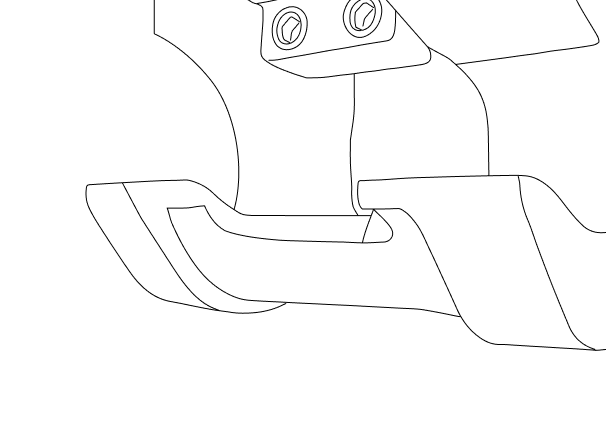
Triple-Lock Safety
Next gen smart connection.
Thanks to our Smart Power Flow Curve and high-quality proportional control valves, you’ll enjoy smooth, fine control during delicate operations and fast, high-capacity performance when the job demands it. All without needing to change a single setting. Unlike competitor systems, there’s no in-cab screen or phone app required.
Select the right configuration for you.
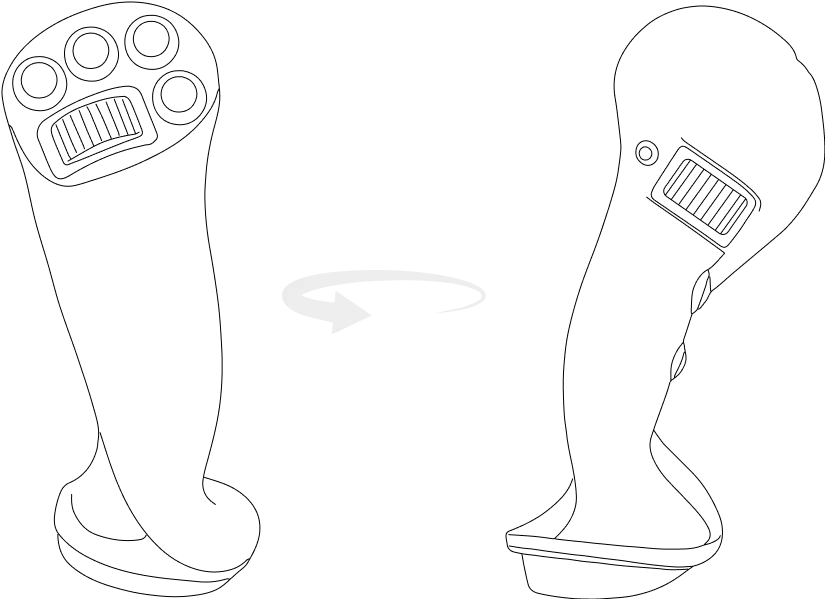
Standard Joysticks
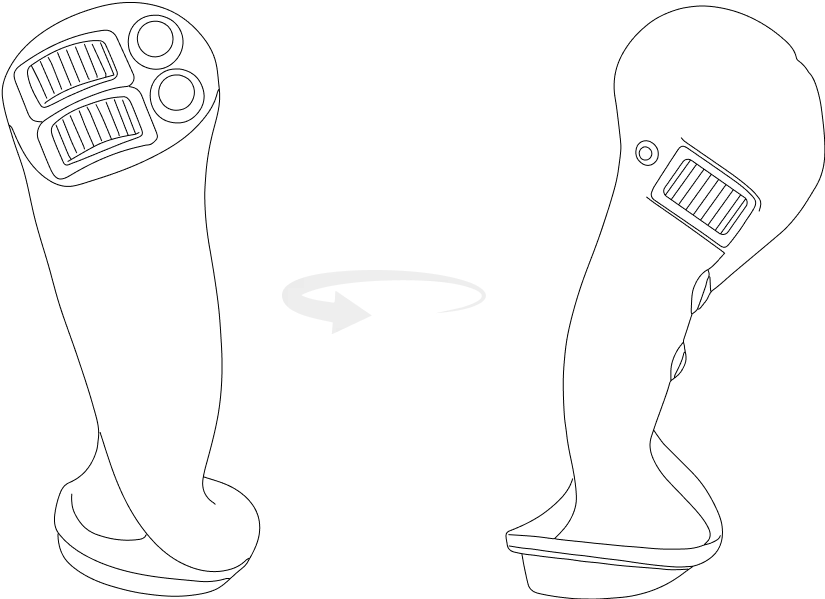
Additional Machine Functions
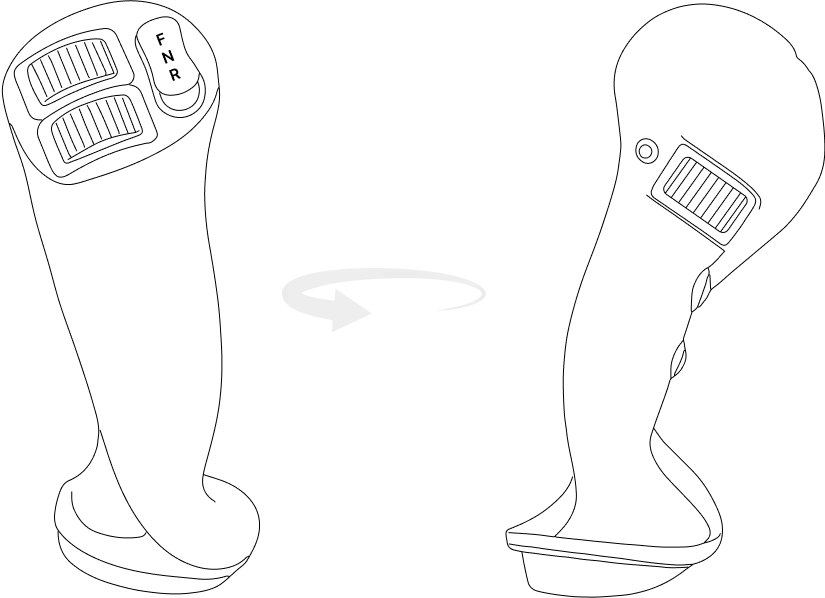
Wheeled Excavator Compatibility
Incredible versatility.
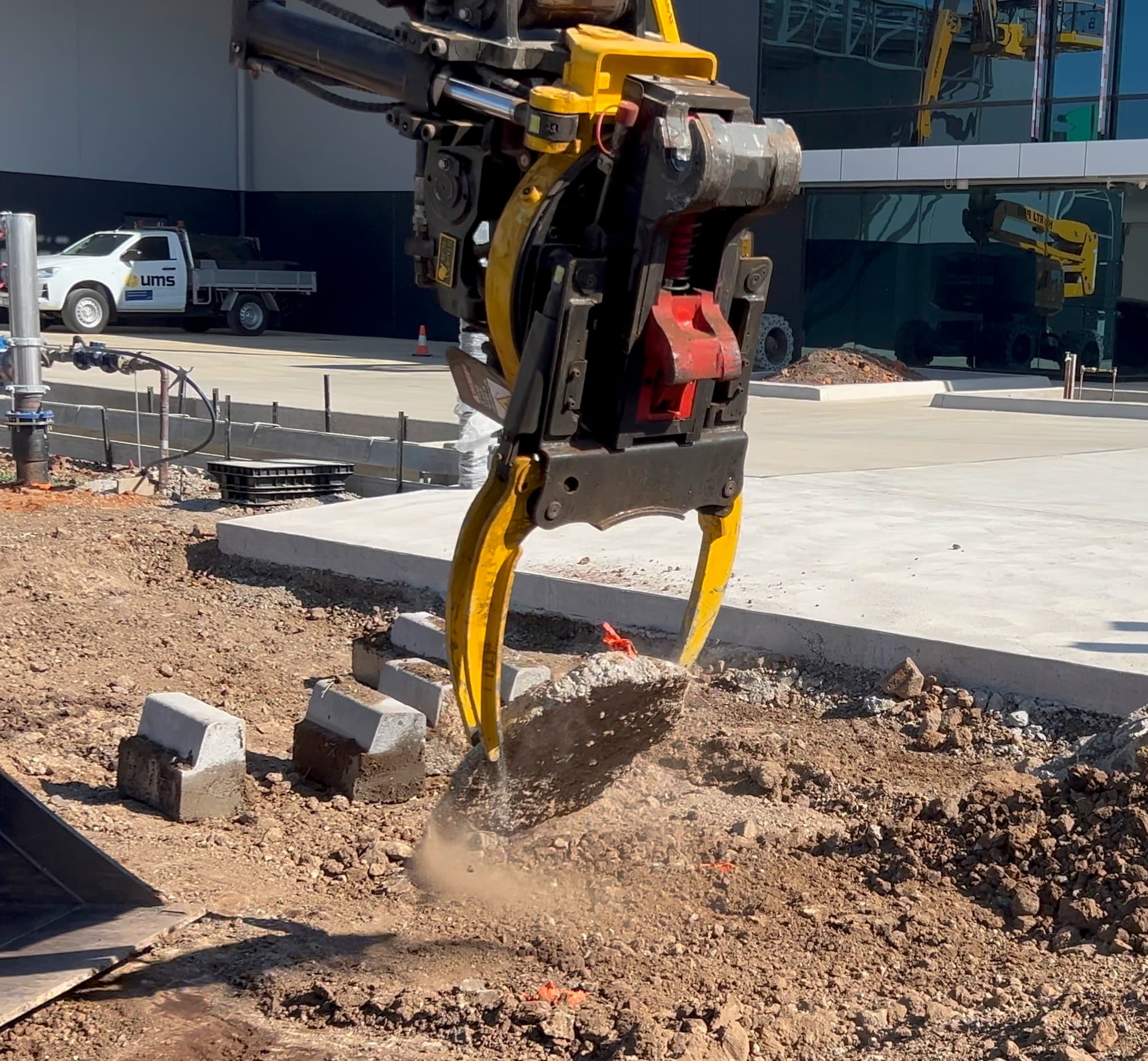
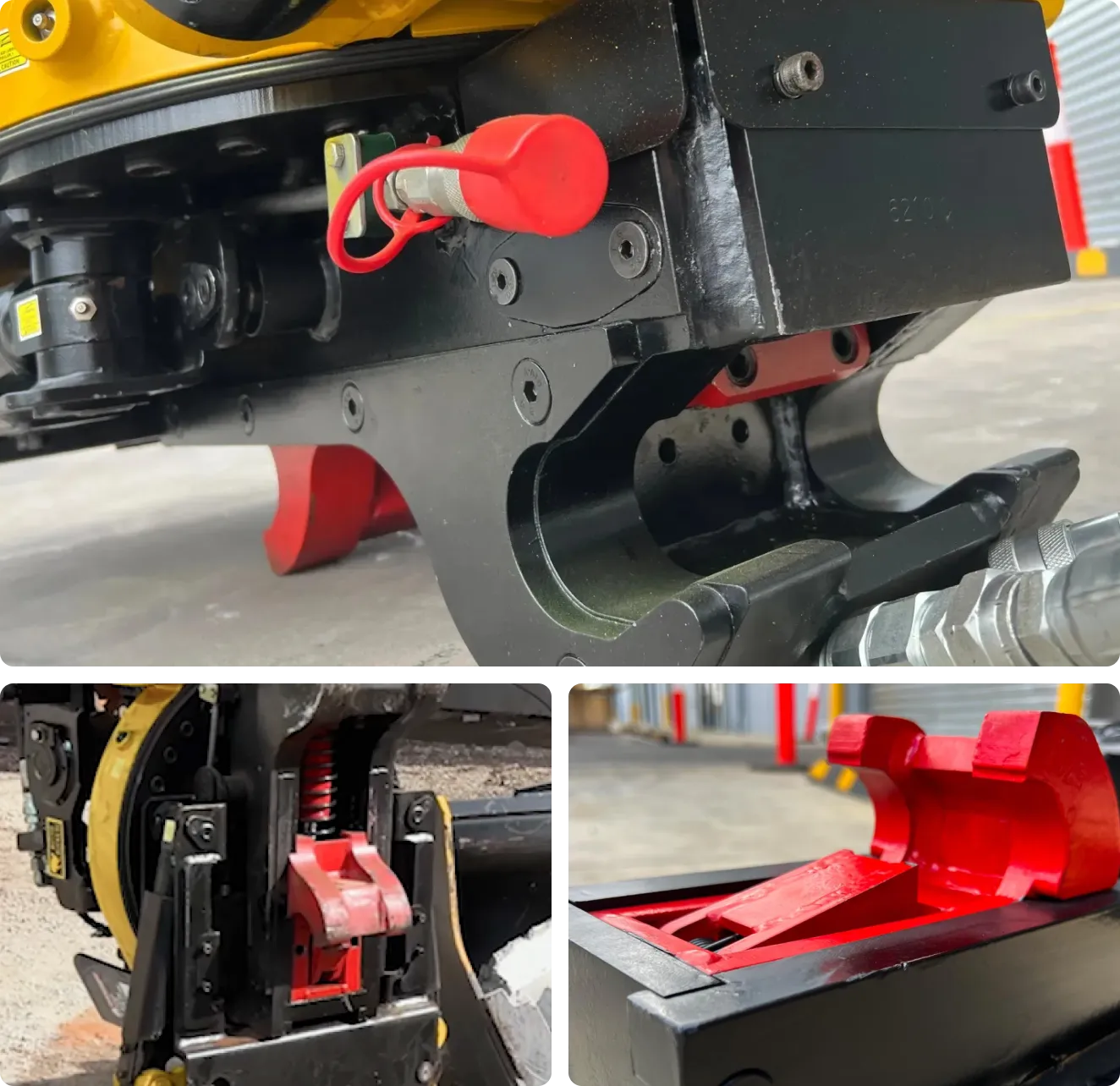
Designed for safe and effecient operations.
Speed-Valve Technology
Speed-valve Technology is an innovative feature that significantly enhances hydraulic efficiency.
By expertly managing the flow of hydraulic fluid within the system, the Speed-Valve can substantially reduce the opening and closing times of the shears, enabling operators to work quicker and more efficiently. This increase in productivity and performance sets the MBI Scrap Shear 3 as an absolute market leader in terms of demanding demolition and recycling projects.
The Speed-Valve also allows for smooth and consistent operation, improving overall user experience.
By providing precise control over the hydraulic flow, the system is under less pressure meaning there is reduced wear and tear on the equipment. This prolongs the life of the shears and minimises maintenance requirements, saving costs for the user and increasing the value of the investment.
Speed-Valve Technology provides the increased efficiency and accurate hydraulic control required to make the MBI Scrap Shear 3 adaptable for many different working environments and conditions.
This adaptability allows operators to confidently tackle diverse demolition and recycling projects, knowing that their equipment is up to the task to perform accurately and efficiently.
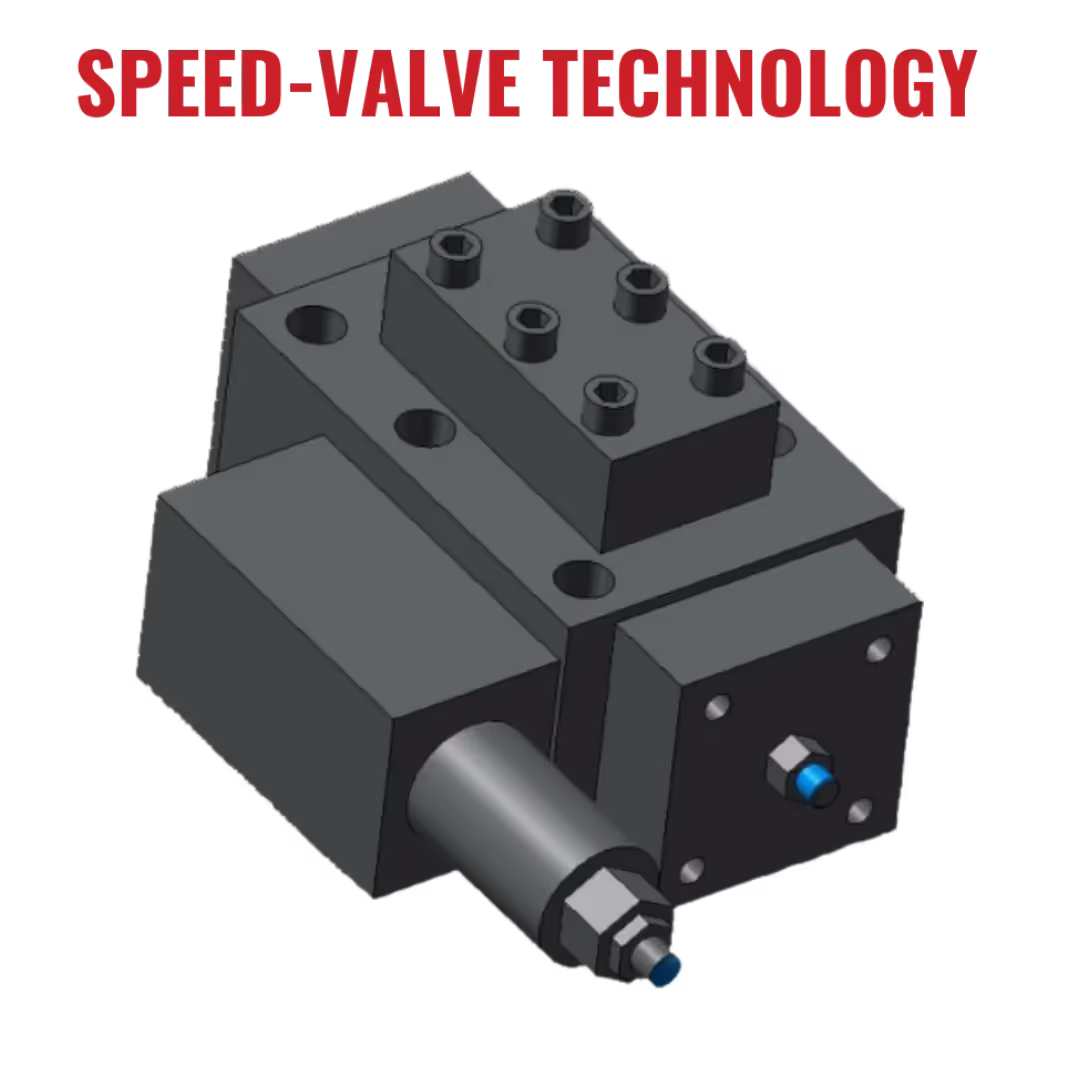
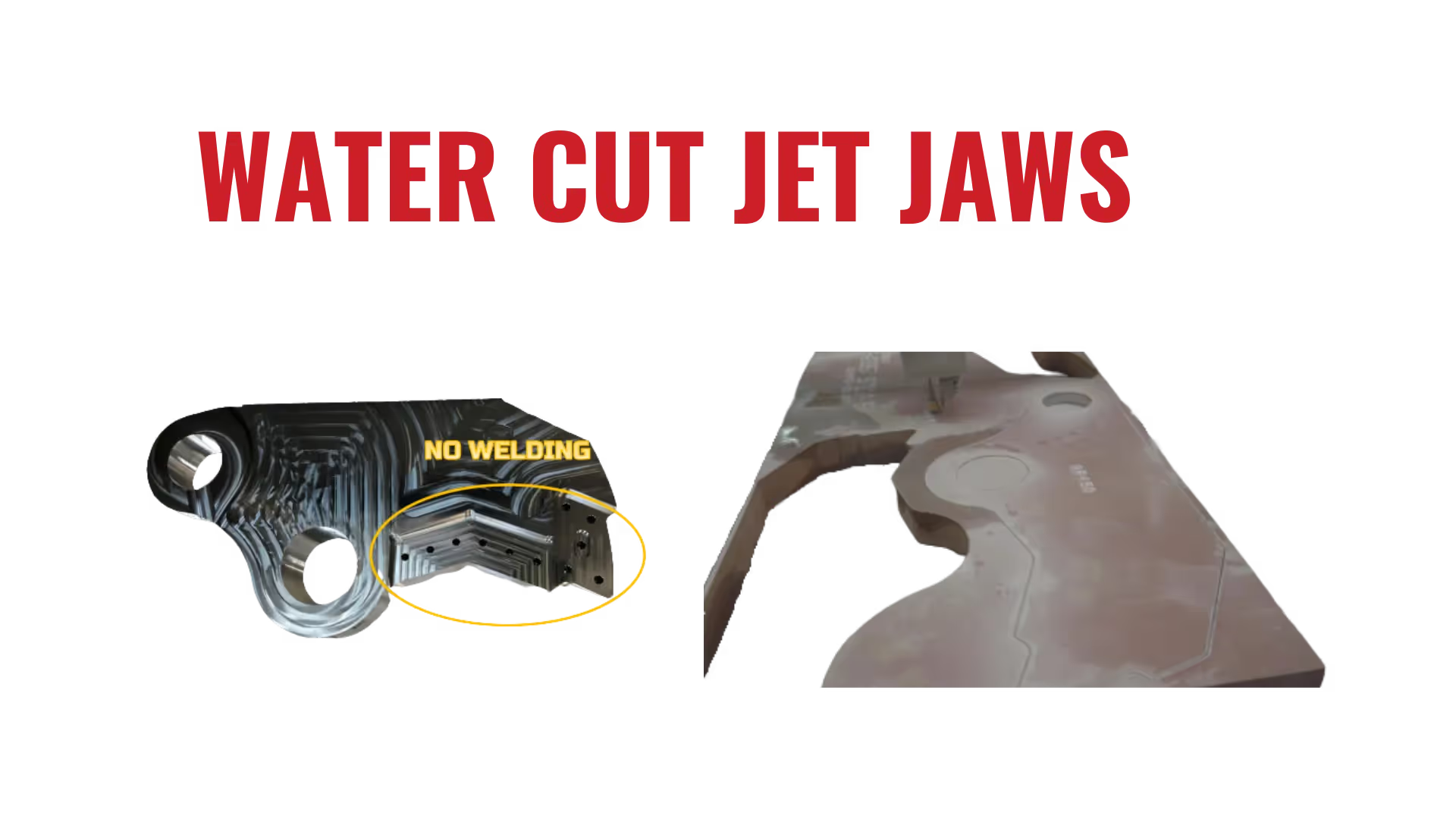
Water Cut Jet Jaws
The MBI Scrap Shear 3 is equipped with water cut jet jaws, a unique manufacturing technique that ensures durability and precision.
Both the lower and upper jaws are precisely cut from 160mm thick HARDOX steel plates using high-pressure water jets, reducing the risk of weakening caused by high temperatures that are associated with traditional cutting processes.
The jaws are milled to retain the steel’s mechanical characteristics, ensuring the shear’s long-lasting durability and resistance to wear.
This process provides additional structural integrity, as well as improving performance through increased cutting capabilities
Armoured Plates
High-wear parts of the shear are fortified with interchangeable HARDOX 500 steel plates. These are installed on the mouth profiles and significantly reduces the need for future maintenance interventions.
The armour plates enable the shear to carry out any cutting process with minimal impact on the main steel structure of the lower jaw, increasing the longevity of the jaw. Additionally, when the plates become worn, they can be easily replaced, reducing cost and downtime.
By reducing wear and tear on the main steel structure of the shear, it enables the continuation of peak performance under even the most demanding projects and tasks. Operators will be able to rely on the shear performing optimally over extended periods of time.
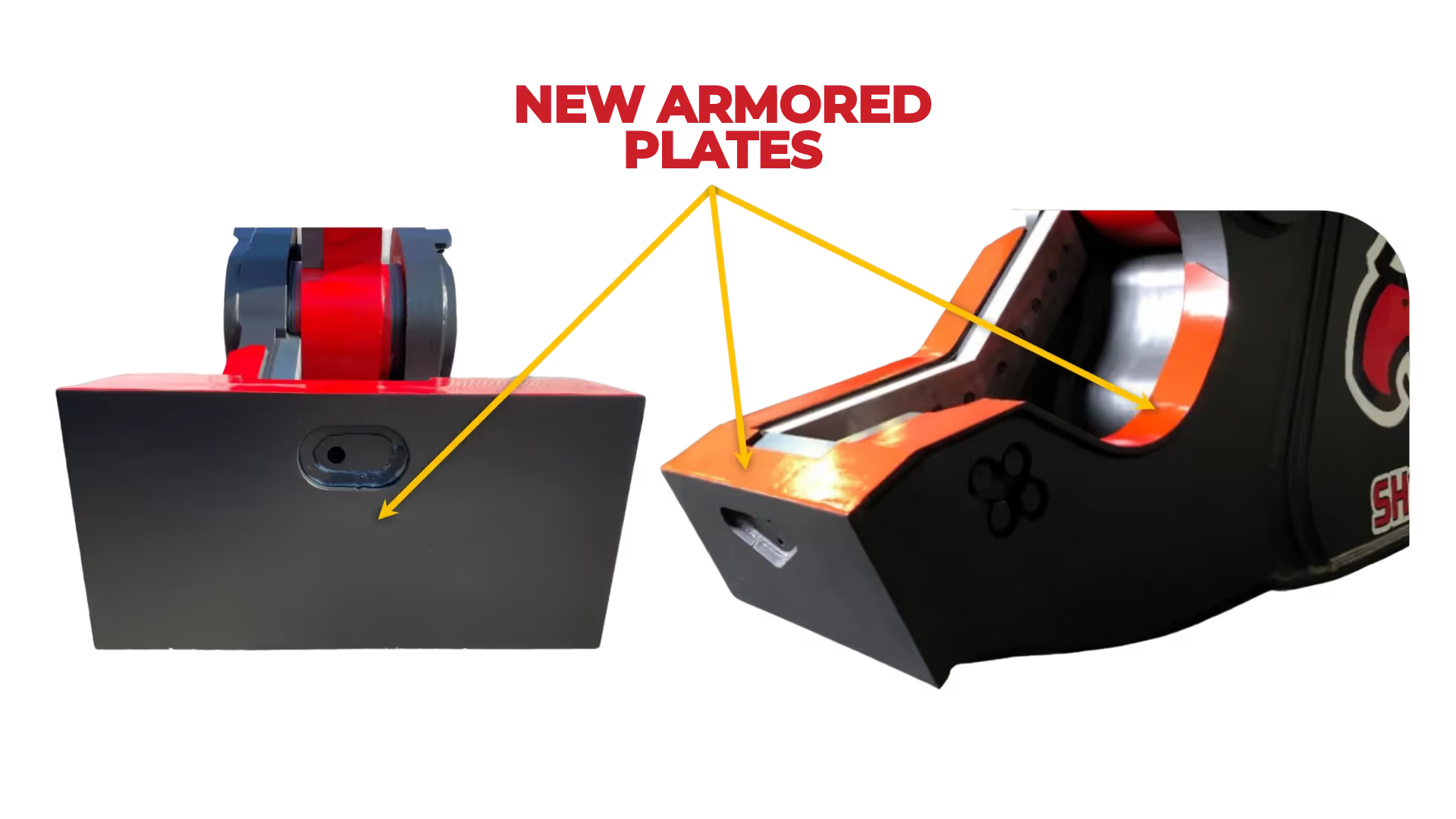
Aussie Buckets x MBI
At Aussie Buckets, we strive for an unwavering commitment to delivering products of exceptional quality and performance. This is the main driver for our collaboration with industry-leader, MBI. Established in 1963, Mantovanibenne, or MBI, has etched its name as a pioneering force in the arena of excavator attachments, specialising in the production of hydraulic attachments for construction, demolition, recycling, and earth-moving sectors. At the heart is the spirit and entrepreneurial vision of its founder, Alberto Mantovani, who has over six decades of experience in the industry.MBI’s approach involves active collaboration with end-users and suppliers to innovate and meet market demands effectively. This ongoing commitment to R&D ensures that their products remain at the forefront of technological advancement, providing the most reliable and efficient solutions for the excavation and demolition industries. They also hold a ISO 9001:2015 certification, which underscores their commitment to maintaining high-quality standards across all their processes.Over the years, MBI has achieved worldwide recognition for it’s quality and innovation - exemplified by it’s global infrastructure with facilities in five countries across the globe - Italy, Bulgaria, France, Germany, and China. This international presence allows them to remain in tune with global trends and demands, further reinforcing their authority as leaders in the industry.